Optimisation de l'assemblage: insert moule et resine de maintien
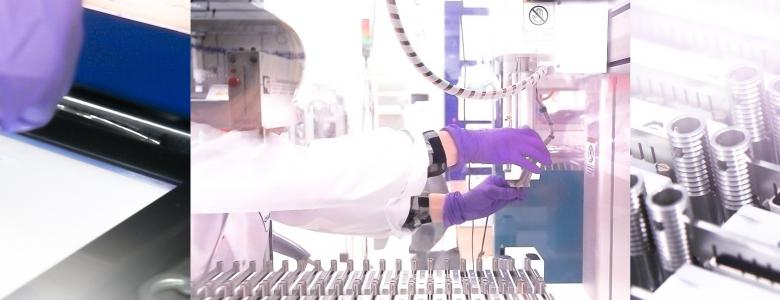
Les connecteurs Nicomatic et tout particulièrement la gamme MIL-DTL-83513G DMM® se doivent d’être de plus en plus aboutis pour être compatible avec les environnements sévères. Pour atteindre cet objectif et dans un souci continu d’amélioration, nous avons pris la décision d’optimiser le processus d’assemblage.
Tout d’abord en profitant de notre savoir faire unique en matière de moulage aquis au fil du temps. L’étape clé a été l’integration récente de l’activité dans notre maison mère à Bons-en-Chablais, en France.
La gamme DMM bénéficie elle aussi de cette expertise. En effet, Nicomatic a investi dans un outillage aussi précis qu’innovant grandement réalisé par des manufactures horlogères de la vallée du Mont-Blanc.
Les tolérances mécaniques atteintes sont de l’ordre de ±0.01mm pour les diamètres et ±0.02mm pour les dimensions hors tout. Grâce à une structure modulaire exclusive, Nicomatic propose l’intégralité des configurations comme un standard. En complément Nicomatic a appliqué la méthode de conception « design for assembly » afin de réduire les temps de changement de configuration à 2h et ainsi contribuer à son taux de livraison dans les délais (OTD) de 97%.
Ensuite en innovant dans la manière d’assurer la rétention de l’insert dans la coque en puisant l’inspiration dans le clavetage mécanique.
La résine époxy est déposée périphériquement depuis l’arrière du connecteur, remplissant une cavité formée d’une pente sur l’insert et d’une gorge dans la coque. Apres polymérisation la résine agit comme une clavette fixe grâce à sa solidité et son pouvoir adhèrent.
En résulte une spectaculaire rétention de l’insert cinq fois supérieure aux exigences de la norme MIL-83513.
Enfin en optimisant le système d’assemblage co-développant pour ce faire une machine 2 axes. Cette dernière est munie d’un système de distribution de résine époxy pour dépose par l’arrière du connecteur.
Un code barre sur la liste de fabrication permet d’analyser instantanément la trajectoire de la tête de distribution et de calculer la quantité de résine nécessaire. L’atelier est maintenu à température fixe ce qui permet de garder constant les paramètres de viscosité et ainsi contribuer fortement à une répétabilité optimum.